Although purchasing metal would appear to be a simple, straightforward task, the alphabet soup of specs, approvals and overall jargon can make it a bit overwhelming. This guide has been prepared to give you the ‘Cliff Notes’ on buying metal.
Section I – Material
- ALLOY – A combination of two or more metals with its own distinct properties.
- ALLOYING ELEMENT – Metallic elements that are added to stainless steel during production to increase hardness, strength, or corrosion resistance.
- AUSTENITIC STEEL – (300 series) Austenitic steels are the most widely used category of steel. Predominantly stainless, these metals containing 16%-26% chromium and up to 35% nickel, usually have the highest resistance to corrosion. They are not hardenable by heat treatment and are nonmagnetic.
- BAR-A form of stainless steel that has been shaped into a long product, either round, square, hexagon, octagon or flat.
- BENCHMARK – Pricing agreement used as a reference among major consumers of ores and alloys.
- BILL OF LADING – Documentation of materials for transportation.
- BLOCK – Metal progressively formed to a desired shape through an impression die.
- BRINELL – Standard test for hardness of metal. The harder the metal, the higher the Brinell number.
- BURR – A burr is a subtle, raised edge or small, generally unwanted piece of material commonly found on a stainless steel strip and formed after a machining operation. This piece can be removed with a deburring tool.
- COBALT ALLOYS – Cobalt alloys feature the ability to maintain magnetic characteristics at higher temperatures than other metals. The high performance alloys are resistant to high temperatures, corrosion and wear, and are often used in the chemical, aerospace, power generation, energy and medical industries.
- COIL – Coils are formed by running a continuous sheet of metal through a roller to accommodate transportation and storage.
- CORROSION RESISTANT STEEL – The addition of chromium not only strengthens an alloy, but also provides a passive oxide layer that essentially seals in the metal. In addition, heat treatment and surface conditioning all contribute to corrosive resistant steel.
- DUPLEX STEEL – Stainless steel made up from a combination of austenitic and ferritic steels that contain high amounts of chromium and nickel. This combination is stronger than both of the individual steels. Duplex steels are a good fit for high strength applications and are highly resistant to corrosion and cracking. They are often used in heat exchangers, destination plants, and marine applications.
- FERRITIC STEEL – Known as the second most widely used steel, Ferritic steels are a class of stainless steel that contain no nickel content. These are magnetic steels that have a low carbon content and contain chromium as the main alloying element, usually between 13% and 17%.
- FLAT ROLLED STAINLESS STEEL – This is a category of steel shapes including sheet, strip and plate.
- GAUGE – The thickness of a particular grade of steel.
- GRADE – The classification of a material based on its composition and physical, mechanical, or chemical properties.
- HI-STRENGTH LOW ALLOY STEEL – HSLA Steel contains less than 5% hardening or strengthening alloys such as nickel, chromium, silicon, manganese, tungsten, molybdenum, and vanadium. Used widely in the oil & gas sector as well as automotive and offshore structural engineering sectors.
- JIT – Just In Time refers to the relatively short amount of time between the receipt of materials and the consumption of them.
- LIGHT-GAUGE STEEL – A very thin sheet of steel that has either been temper rolled or passed through a cold reduction mill.
- MARTENSITIC STEEL – A small category of magnetic steels typically containing 12% chromium, a moderate level of carbon, and a very low level of nickel. This type of steel is heat-treatable and can provide hardness and strength in a wide range.
- NICKEL – Nickel is a naturally occurring, lustrous, metallic element. It is the fifth most common element on earth and occurs extensively in the earth’s crust. Nickel’s main characteristics include a high melting point, 1453°C, resistance to corrosion and oxidation, and magnetic at room temperature.
- NICKEL PIG IRON – NPI was developed by Chinese steel makers as an alternative to pure nickel in the production of stainless steel. Low grade nickel ore, coking coal, and a mixture of gravel and sand are used instead of pure nickel. Sometimes referred to as dirty nickel, NPI emits a particularly high amountof carbon dioxide during production. This cheaper substitute for nickel influences the price of nickel on the world market by lowering the demand in certain applications.
- PH GRADES – (17-4PH, 17-7PH) Precipitation hardening grades are soft and ductile in the solution annealed condition, and are capable of high properties with a single heat or aging treatment. Precipitation hardening stainless steels provide remarkable levels of high strength and hardness in a very wide range.
- PLATE – Stainless steel with a thickness of 3/16″ or more and generally a width of ten or more inches.
- PRODEC ® STEEL – Prodec is a unique version of austenitic stainless steel which is produced for enhanced machinability and exceptional uniformity. It offers faster machining speeds, longer tool life, improved part quality, and a lower total cost of machined parts.
- SHEET – Stainless steel with a thickness of less than 3/16″ and generally a width of 24 or more inches.
- SPECIALTY STEEL – Higher specification category of steel that includes electric, alloy, stainless, and tool steels. They are normally high in carbon or other alloys.
- STAINLESS STEEL – Corrosion resistant steels containing at least 10% chromium which imparts remarkable resistance to corrosion and heat.
- SURCHARGE – Surcharges are price adjustments levied by steel producers in response to price/availability fluctuations of raw materials and energy used to manufacture its products. These minor price adjustments are made monthly in lieu of adjusting contractual price agreements.
- TEMPERS -Tempering optimizes hardness without excessive brittleness. Strength, stiffness and ductility are classified by degree of Rockwell Hardness. Half Hard or Rockwell B-70 – B-85 can be bent 90° the direction of rolling around a radius equal to its thickness. Quarter Hard or Rockwell B-60-B-75 can be bent 180° across the direction of rolling over one thickness of the strip and 90° in the direction of rolling around a radius equal to its thickness. Full Hard or Rockwell B-84 – B90 is not intended for cold rolling.
- TOLERANCE – Dimensional limits of deviation from a desired measurement.
Section II – Process
A variety of technical explanations are associated with the processing of metals. We’ll run through them in terms you can understand.
- ANNEALING -The process of heating cold stainless steel to yield a greater amount ductility and softness and to increase corrosion resistance.
- BRUSH FISNISHING – Surface imperfections are removed from material through the use of an abrasive belt or wire brush. The result is a uniform, parallel grain surface texture.
- BUFF POLISHING – A cloth wheel is used to buff a material’s surface, removing imperfections and creating a glossy sheen.
- CHAMFERING -The process of machining an angled edge, removing sharp corners from a part.
- CUT-TO-LENGTH – A cut-to-length line will uncoil the material, level it, and then cut it to the required length and stack it.
- DEBURRING – Removing the small ridges, sharp edges or imperfections from a strip of metal that resulted from slitting, shearing or blanking. The process can involve sanding, brushing, abrasives, blasting and polishing.
- DEEP DRAWING – A sheet metal blank is drawn into a forming die by the mechanical action of a punch, yielding a shape that is longer than it is wide.
- EDGING – Strips of steel may require specific edge conditioning and are rolled to smooth the edges and remove burrs.
- FACING – Producing a flat surface on a part by removing metal from the end of a work piece, usually a cylindrical form.
- FINISHING – The exterior of a metal product is treated creating a complimentary layer to its surface. Finishing options may include plating, powder coating, blackening, brushing, polishing or grinding.
- FORMING – Changing the shape of stainless steel by adding pressure or force, without removing or adding any material. Also known as cold forming, hot forming or wire forming.
- GRINDING – Grinding uses friction to smooth the surface of a metal part.
- HYDROFORMING – High pressure hydraulic pumps press fluid against a material and into a die to mold it into a desired shape.
- LASER CUTTING – Laser cutting uses a beam emitted from a laser tube reflected by mirrors in the laser head and a lens that finely focuses the beam onto the material surface for precise cutting.
- LEVELING – A leveling line processes sheet producing a material that is smooth, flat and relatively free of internal stresses.
- PLASMA CUTTING – In plasma cutting, a column of electrically charged gas creates a high-energy arc, which melts the material being worked in a narrow path.
- PLATING – A manufacturing process in which a thin layer of metal coats a substrate. Achieved either through electroplating or by an autocatalytic chemical process, plating is added for decoration, corrosion resistance, to harden or alter conductivity, improve wearability, or increase magnatism.
- POWDER COATING – Dry plastic powder is meted onto the material to produce a decorative finish coating. It is a highly effective method of removing surface defects.
- ROLL FORMING – Roll forming involves a long strip of metal passing continuously through consecutive sets of mounted rolls each performing an incremental bend, until the desired profile is obtained.
- SAND BLASTING – Sand or other abrasives are forced into a substrate at high speed, creating a uniform, matte finish texture.
- SHEARING – Shearing is the process used to cut straight lines on flat metal stock. Using an angled moving blade, the shear cuts progressively across the sheet in a guillotine-like action.
- SLITTING – Slitting is the process of cutting larger width coils into narrower width coils to meet a customers’ demands.
- STAMPING – Stamping changes the shape of a metal part as it comes into forced contact with punches or dies. Metal stamping machines cast, punch, cut and shape metal sheets.
- WATER JET CUTTING – A waterjet uses a high pressure stream of water combined with a granular additive. As the pressurized mixture passes through a small diameter nozzle, it forms a coherent jet of abrasive/water moving at very high speeds which will erode a narrow line in a stock material.
Section III- Quality Standards & Certification
How To’s for designers, manufacturers and users; They promote safety, reliability, and operational efficiency which can be vital to customers who ultimately purchase material.
- ASME STANDARDS – A series of performance test codes, standards for boiler pressure vessel and nuclear quality assurance.
- AS9100 – Quality management system standard applicable to companies that supply to aerospace and defense industries.
- ISO 9000 – A worldwide recignized stand that addresses quality management and provides tools for companies to ensure their products and services consistently meet customer requirements. ISO 9001:2008 sets criteria for quality management and includes principles for customer focus, management and continuous improvement.
- MTR – Mill Test Reports are quality assurance documents used in the metals industry that certify a material’s chemical and physical properties are in compliance with international standards of the manufacture and process of raw materials.
- NADCAP – National Aerospace and Defense Contractors Accreditation Program, assesses special processes of suppliers using a standardized approach based upon industry consensus.
- TQM – Total Quality Management solutions for automating critical business processes including corrective actions and risk assessments to enhance productivity and streamline quality operations.
Section IV – Association
- AIAA – American Institute of Aeronautics and Astronautics www.aiaa.org
- AISC – American Institute of Steel Construction www.aisc.com
- AISI-American Iron and Steel Institute www.steel.org
- ASD-Association of Steel Distributors www.steeldistributors.org
- ASM – American Society of Metals www.asminternational.org
- ASME – American Society of Mechanical Engineers www.asme.org
- ASTM – American Society for Testing and Materials www.astm.org
- AWEA-American Wind Energy Association www.awea.org
- AWS – American Welding Society www.aws.org
- FMA- Fabricators & Manufacturers Association www.fmanet.org
- LME -The London Metal Exchange www.lme.com
- MSCI – Metal Service Center Institute www.msci.org
- NAM – National Association of Manufacturers www.nam.org
- NAAMM- National Association of Architectural Metal Manufacturers www.naamm.org
- PMA-Precision Metalforming Association www.pma.org
- SAE – Society of Aerospace and Automotive Engineers www.sae.org
- SMWIA – Sheet Metal Workers International Association www.smwia.org
- SSINA – Specialty Steel Industry of North America www.ssina.com
- TMS – Minerals, Metals and Materials Society www.tms.org
Sources: ISO, Metal Bulletin, Platts McGraw Hill Financial, Outokumpu, Stainless Steel World, The Stainless Steel Information Center, Thomas Net
GET IN TOUCH WITH US TODAY
If you have a project in mind, would like to see our prices, or simply want to check out our inventory in person; good news. We have factory tours and a showroom to help you plan out your current or future project. Call us up and talk to any of our friendly staff and ask us about our current schedule, or to explore ways we may be able to help you with your goals. If you’d like to see our latest projects, explore our inspiration gallery or follow us on Instagram, where we ongoingly post our latest completed projects.
Click the live chat at the bottom of the browser window and connect instantly with our team of experts.
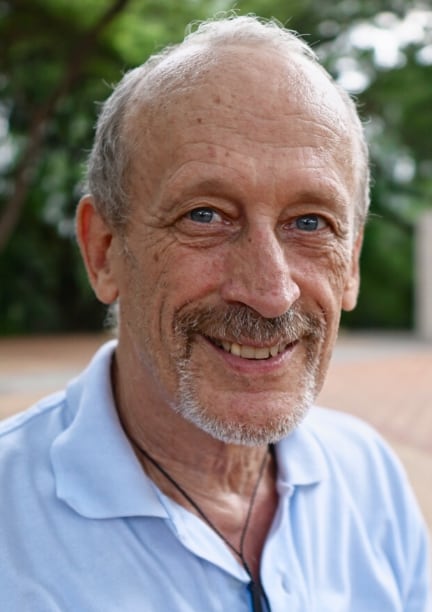
Dan’s very enthusiastic about our products and is a true ambassador for our styles and quality.